Повесть о настоящем сабвуфере
- "Январь - июль.
Строил надежный туалет.
Тщательно все обдумав, начал пока одно очко."
Д.Шинкарев
"Первенький" в этой машине сабвуфер был исполнен на базе советских,основательно уже позабытых головок 10ГД30 - в семидесятых - рабочей лошадке отечественной электроакустики. При пристойной резонансной частоте (32 Гц), они обладали жуткой добротностью, порядка 0.8 - 0.9 (по разным оценкам), поэтому обладали изрядной отдачей, но сильно горбатой частотной характеристикой. Ну да что там, надо ввязаться, а там посмотрим (оригинал высказывания Ons'engage, pius on verra принадлежит Наполеону Бонапарту, которому автор высказывает свою признательность за продуктивный тезис).
В результате вышел ящик объемом около 20 л, почти прямоугольный (обращенная к спинке заднего сиденья стенка, понятно, была сделана с соответствующим скосом), с двумя головками на передней стенке и усилителем, прихваченым к боковой.
Басила эта штука низко и охотно, но не очень музыкально, в смысле явной предрасположенности к определенным тонам и явной нелюбви к другим, независимо от произвола музыканта, который эти ноты брал.
Некое улучшение наступило после переделки в изобарическую конструкцию, путем установки еще двух таких же головок (все, больше не осталось). Получившееся чудовище - на снимочке. Душа, однако, просила другого - уважения к музыкантам, вооруженным басовыми инструментами. Они ведь чем-то думают, прежде чем дернуть за струну или нажать на педаль колотушки. Новый сабвуфер был задуман на базе 25 сантиметровой головки фирмы a/d/s/. Я ее слышал в фирменном демонстрационном автомобиле на соревнованиях и мне понравилось. Задач при проектировании ставилось две:
- Получить частотку, согласованную с функцией передачи салона
- Сделать сабвуфер, составляющий минимальную помеху при обыденном использовании автомобиля, а точнее - его багажника.
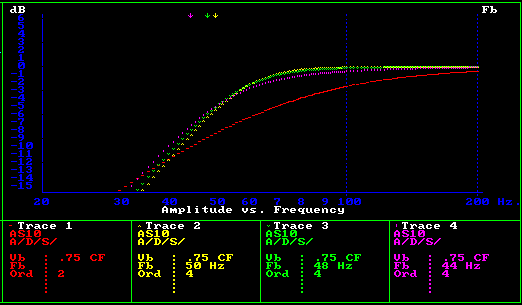
Требуемый объем оказался около 19 л, из чего и исходили. Красная линия на графике - для сравнения, что бы получилось с этой же головкой в таком же объеме при закрытом ящике. Забегая вперед, скажу, что не так-то просто его было сопоставить с реальной конструкцией, из-за некоторой экзотичности форм.
Теперь об исполнении. Поскольку машина - хетчбек (античный Форд Сиерра,я не говорил?), полновесное использование достоинств багажного отделения возможно лишь при условии, что ничто не мешает сложить сиденье. В этих предпосылках взгляд упал на правый задний угол багажника, причем, поскольку боковая поверхность там далеко не плоская, это означало необходимость некоторого изыска в выборе материалов и технологии. Темное прошлое автора включало, на некотором этапе, возню с катерами и моторными лодками, поэтому вид стеклоткани и запах ненасыщенных полиэфирных смол его (меня, если вы потеряли нить) не пугал. Так и порешили.
Итак, этап первый и важнейший. Памятуя о пропорции 7:1 между измерением и обрезанием, для всех плоских деталей, которые предполагалось изготавливать из доброй старой ДСП, были сделаны шаблоны из оргалита, которые постепенно,прямо по месту в багажнике, подгонялись до получения максимальной конформности,то бишь отсутствия зияющих зазоров.
Затем по полученным шаблонам были вырезаны все панели, кроме задней,обращенной к стенке багажника, и лицевой (это придет потом) и соединены по всем правилам - клей, шурупы, бруски и косынки подкреплпения и т.д.. Детали обивки (две), по которым предстояло выклеивать стеклопластиковое дно ящика, были извлечены из автомобиля и временно закреплены на листе фанеры в том же относительном положении, которое они занимают в багажнике.
Теперь главная задача - защитить их от всепроникающей смолы. Отличный материал для этого - полиэтиленовая пленка для упаковки продуктов. Она тонкая и липнет сама к себе, что дает некоторую уверенность в отсутствии мест возможной протечки смолы, последтвия чего имеют природу катастрофы. После того, как все было закрыто (в два-три слоя - пленка тонкая и форм не искажает), деревянная часть ящика была поставлена на место, а все стыки с обивкой снаружи заклеены рыжим упаковочным скотчем.
На рисунке видны первые слои стеклоткани, уложенные по поверхности защищенной обивки, играющей в этой технологии роль матрицы. Когда они затвердеют, можно отодрать скотч, вытащить ящик из обивки ( если вы были аккуратны с разделительной пленкой. Если нет - то тоже отодрать, с заметно большим ущербом), поставить обивку на место и работать уже с корпусом сабвуфера как таковым.
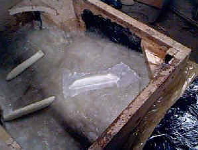
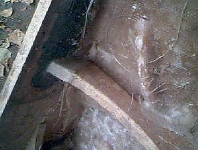
и могучая промежуточная стенка, соединяющая две боковые (ДСП) и заднюю (стеклопластик).
В этом жанре - много не бывает. После того как вся структура прочностью и статью станет напоминать линкор (на меньшее не соглашайтесь), можно угомониться и, перед тем как поставить лицевую панель, с уже вырезанными дырками под голвку и тоннель (или тоннели, как в моем случае), покрыть всю поверхность изнутри вибропоглощающим материалом. Почти любое антикоррозийное покрытие в аэрозоле подойдет.
После окончательной сборки корпуса, выравнивания неровностей на стыках и раковин (неизбежных, увы) на стеклопластике все вышеизложенное приобретает такой вот вид (с лица и со спины).
Остается самое приятное - отделка, установка и подсоединение головки и победное завершение эпопеи. Результаты - на снимке. Торчащие из тоннелей серые ПХВ трубы использовались при доводочной настройке фазонивертора и вскоре исчезли внутри.
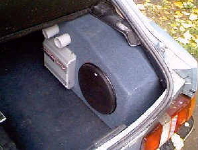
P.S. Спустя положеннное время прекратил свою земную жизнь и автомобиль, но, что интересно: корпуса сабвуфера до сих пор жив (в личном музее автора), а усилитель Jensen продолжает свою боевую жизнь, и приносит награды за убойные уровни звукового давления на машине Серегя Клевцова.
На правах рукописи